Battery Simulator HPDC 1000 BattSim
The DC battery simulator serves as a replacement for the high-voltage vehicle battery for operating the vehicle under almost real conditions on vehicle test benches (reproducible road driving simulation). The system is operated in 2-quadrant operation (source/sink).
The DC battery simulator is preferably connected to the AFE converter (energy control cabinet) of an existing test bench system. By integrating (expanding) the DC battery simulator into the existing test bench infrastructure, costs can be saved accordingly. If the connection to an existing system is not possible, an extra DC link feed unit can also be supplied.
The future oriented, modular, compact AIP System design offers both, IGBT and SIC technology, and AIP can equip the power electronics with the technology, as required.
Multi-channel design of the BattSim / BattTest systems
Systems can be designed as 2-channel with a total of up to 4 DC outputs, of which 2 DC outputs can be used simultaneously. Relevant e.g. for test runs with front axle/rear axle or additional charging function.
DC intermediate circuit
Advantages: Cost savings, Reduction of the required AC connected load, utilization of the simultaneity factor for efficient test system operation, compact system design, demand-oriented power distribution to individual test systems, reliability of the DC-side supply.
Example: 600 kW HPDC-BattSim Energy System in Connection with a 4WD Chassis Dynamometer
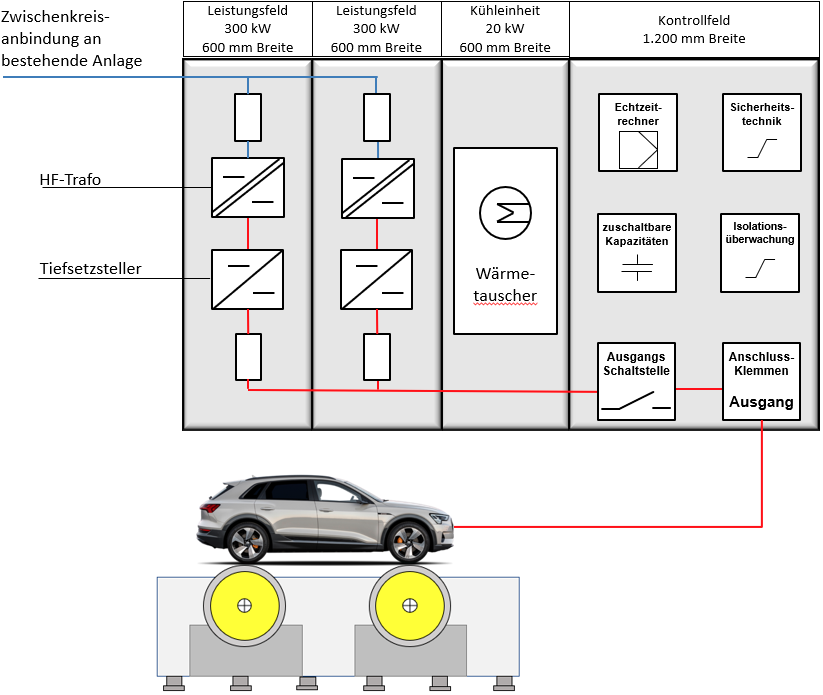
Technical Data
Performance classes |
200 … 1,200 |
kW |
Output voltage range |
20 … 1,200 |
V |
Current |
300 … 1,800 |
A |
Overload capacity for 30 s |
150 |
% |
Real-time control system |
10 |
kHz |
Current rise time |
<1 (with setpoint jump 0% → 90%) |
ms |
Current accuracy |
0.05 |
% MW |
Voltage rise time |
<5 (with setpoint jump 10% → 90% with 500 uF load) |
ms |
Voltage accuracy |
0.05 |
% MW |
Dimensions (W x D x H) |
2,200 … 5,400 x 2,200 x 600 |
mm |
Applications
- Simulation of the vehicle battery, e.g. for
- Endurance tests
- Performance tests for the entire vehicle
- Highly dynamic performance/load tests of electric drive systems
Advantages
- Modular, expandable power range from 200 … 1,200 kW
- Connection to the existing intermediate circuit of the motor converter of the test bench
→ no additional feed necessary
- Highly dynamic and precisely regulated power electronics
- High efficiency
- Very compact design (300 kW per power field)
- Integration into the existing security matrix